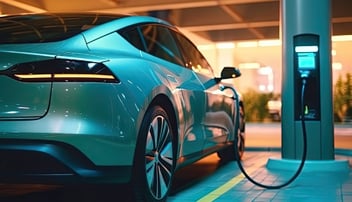
The Case for Styrene-Butadiene Emulsion Polymers in Pressure Sensitive Adhesives
A pressure-sensitive adhesive (PSA) is a material that holds two substrates together solely based on surface contact, which is achieved by slight initial external pressure. Most commonly encountered in the form of adhesive tapes, PSAs are favored..
A pressure-sensitive adhesive (PSA) is a material that holds two substrates together solely based on surface contact, which is achieved by slight initial external pressure. Most commonly encountered in the form of adhesive tapes, PSAs are favored because their application can be automated and requires no specialized equipment. They also save time in assembly operations because, unlike liquid adhesives, they don’t have a long setup and don’t need to be cured. The bond itself in a PSA is automatic, and can be used on many surface types, from wood to glass, making it a versatile solution for adhesive tapes, food labels, packaging, bandages, and electronics.
Though they are applied differently, all pressure-sensitive adhesives exhibit three defining characteristics: adhesion, cohesion and tack. Adhesion and cohesion both describe molecular interactions but in different ways. Adhesion refers to how well the molecules of two different materials bond, while cohesion refers to how well the molecules of a single material bond together. So, adhesion measures the stickiness of an adhesive when peeled from a surface; cohesion measures the stiffness of an adhesive. Tack, on the other hand, refers to how aggressively an adhesive grabs a surface after brief contact. These three properties often work in opposition to one another and optimizing them involves making tradeoffs. For instance, increasing tack and peel comes with a drop in shear and vice versa. Synthesis chemists and formulators work to balance these properties and achieve the desired strength and capabilities for their application.
Because PSAs are made from polymers, adhesion, cohesion and tack are determined by the properties of the polymers used in the formulation. In this blog, we will explore different polymer systems used in the production of PSAs and discuss why styrene-butadiene emulsion polymers are emerging as great building blocks for the development of the next generation of PSAs.
Stick with us — we’re going to start with the most common ways to make PSAs.
Manufacturing Methods for Pressure Sensitive Adhesives
Tape manufacturers, depending on the application, will choose from one of four main processes in the development of their PSA. It’s the variety of manufacturing methods, combined with different chemistries, that yields so many different types of PSAs with varying performance characteristics.
Solvent-based Methods
In this method, adhesive components (often rubber or acrylic) are dissolved in a solvent before they are coated onto a web. After this, the solvent is then evaporated using air and heat, leaving the adhesive behind. Adhesives produced using solvents are high performing, though they are expensive and time-consuming to make. Also, the solvents used can be safety hazards and therefore require careful disposal.
Hot-melt Methods
The hot melt process consists of a mixture of polymers (usually thermoplastic polymers), resins and a diluent, which are heated until the mixture is flowing. This mixture is then applied to a web and wound onto a roll. A special release layer allows the tape to easily unwind off the roll, and an aggressive adhesive layer provides high levels of stickiness. Hot melts are less expensive than solvent-based adhesives, though they do not perform as well under high temperatures.
UV-curing Methods
These adhesives are made without the use of solvents or other volatile compounds, so they are environmentally friendly. They cure rapidly when exposed to UV light and at lower temperatures, which means they can be used on heat-sensitive substrates. Minimal shrinkage, durability, strength and resistance to outside elements are all benefits associated with UV-curable adhesives.
Emulsion-based Methods
Emulsion-based adhesives use water as a medium to disperse the polymers and coat them onto a web. The water is then evaporated by means of heat and air to leave behind the adhesive. Emulsion-based PSAs are versatile, providing a range of options to accommodate varied performance requirements. Plus, they don’t use strong solvents, so manufacturers can avoid stringent processing restrictions.
Currently, acrylic is the most common emulsion polymer used in PSAs. In North America, 30% of adhesives rely on pure emulsion-acrylics. Styrene-butadiene (SB) emulsion polymers, by contrast, make up just 3% of the North American adhesives market. Interest in SB-based PSAs is growing, however, because of their unique performance characteristics. Up next, we’ll compare acrylic to SB as a building block to produce adhesives.
Styrene-Butadiene vs. Acrylic Adhesives
Acrylic emulsion adhesives are a common pressure sensitive adhesive formulation for good reason. They have good initial tack, excellent adhesion and broad temperature performance on a variety of substrates. They also provide lower operating temperatures, better UV stability and improved clarity over other formulations. Many of these characteristics are related to acrylic’s good adhesive wet-out, which refers to a material’s ability to flow and cover a substrate to maximize the contact area and the attractive forces between the adhesive and bonding surface.
Styrene-butadiene emulsion polymers introduce different properties, mainly because of the butadiene’s propensity to crosslink, which occurs when polymer chains connect to each other through covalent bonds. The level of butadiene crosslinking is controlled to achieve varying levels of crosslink density between polymer grades. Crosslinking increases tensile, stiffness, and shear strength. Another benefit offered by SB polymers is their lower polarity compared to acrylics, which improves their water resistance properties. As the table below illustrates, SB adhesives accentuate certain properties that acrylics don’t and vice versa.
Styrene-Butadiene Adhesives |
Acrylic Adhesives |
Wider Tg Range (-85 to 100°C) |
Wide Range of Monomer selection |
Shear Performance |
Higher Tack and LSE Adhesion |
Crosslink Density and Modulus Control |
Higher Polarity, HSE Adhesion |
Tensile/Elongation Balance |
Morphology Control |
Water Resistance |
Higher Solids |
High Filler Acceptance |
More UV and Oxidation Resistant |
In dynamic mechanical analysis (DMA) testing, the differences between acrylic and SB adhesives becomes clearer. DMA measures the viscoelastic performances of a polymer — i.e., the potential elastic or viscosity-related capabilities of the system. To conduct the test, a thin sample of adhesive is placed between two metal shafts. As the bottom shaft oscillates, the top shaft measures the amount of energy transmitted through the sample. DMA evaluates polymer performance as one variable — either temperature or frequency of oscillation — is changed over time. The variable temperature method (-80° to 200°C) is the most commonly used method in adhesive analysis.
The DMA curve below shows the results of an acrylic adhesive versus an SB adhesive. Superimposed on the curve is glass transition temperature (Tg) data measured using differential scanning calorimetry (DSC). According to DSC data, the Tg of acrylic and SB adhesives are about the same.
Notice that the left vertical axis is measuring a value known as storage modulus, indicated by the symbol G'. The right vertical axis is measuring Tan delta, indicated by the symbol δ. The storage modulus represents the solid part of the polymer (pure elasticity). It has a companion measure known as the loss modulus, G", which represents the liquid part of the polymer (pure viscosity). Tan delta is the ratio of G" to G' (viscosity/elasticity), providing information on how well a polymer recovers after deformation.
In a typical DMA temperature scan curve, there are two important sections in modulus measurement: a glassy region at low temperatures, where G' (storage modulus) is high, typically above 100 MPa; and a rubbery plateau, where G' is the dominant factor and the compound behaves as an elastic solid with adhesive properties. As a rule of thumb, polymers exhibit tack when G' is below approximately 300 KPa, which is known as the Dahlquest’s tack criteria.
The other important information DMA provides is the Tan delta, which exhibits a peak around the thermal glass transition of the polymer. The graph above reveals that styrene-butadiene adhesives have a wider glass transition period compared to acrylic adhesives, as well as a multimodal distribution of glass transition peaks. These differences account for the unique properties of an SB emulsion polymer’s molecular architecture and distribution of styrene and butadiene within the polymer chains. SB adhesives have improved tensile strength, improved water resistance and improved shear and peel. The tack of SB adhesives is lower than acrylic adhesives, but they still have decent tack. The SB adhesives can also be further formulated with dispersion tackifiers to increase the level of tack and peel.
The improved performance properties of SB adhesives vs. acrylic adhesives can be seen in the data below.
Choosing the Right Emulsion Polymer for Your PSA Adhesive Application
Though acrylic adhesives continue to dominate the industry, the case for styrene-butadiene adhesives is getting stronger, especially as the increasing demand for newer, better PSA solutions drives innovation in adhesive technologies. In the end, though, it depends on your application and the properties you’re trying to target. Mallard Creek currently offers a range of styrene-butadiene emulsion polymers for use in adhesives. For example, Rovene 4813 and Rovene 4848 are very soft, non-carboxylated SB emulsions that provide a good balance of tack, peel and shear. Rovene 9410 and Rovene 6130 are great choices for use with tackifiers.
And, of course, we can help you develop custom formulations. Our team of polymer chemists will work with you every step of the way to develop the right adhesive for your specific application. Contact Mallard Creek Polymers today to start a conversation.
