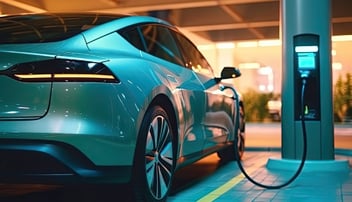
At Mallard Creek Polymers, we have built a globally-respected business on delivering the finest emulsion polymer formulations for our clients in multiple industries for hundreds of applications. People often ask us, “What’s the difference between..
At Mallard Creek Polymers, we have built a globally-respected business on delivering the finest emulsion polymer formulations for our clients in multiple industries for hundreds of applications. People often ask us, “What’s the difference between emulsion polymers and solution polymers?” This article will offer a little clarity on the differences between these two manufacturing mainstays.
Definitions
Let’s start with a definition for polymerization itself. Polymerization, as a chemical reaction, may occur with solids, liquids, or gases. Since solid state reactions are slow, and since gas-phase reactions require high temperatures (which leads to instability when trying to achieve a high molecular weight), you see these states of matter neglected in manufacturing, where liquid-state polymerization reigns supreme.
There are actually four common types of liquid-phase polymerization reactions. Homogeneous reactions include bulk/mass polymerization and solution polymerization, while heterogeneous reactions include suspension/pearl/bead polymerization and emulsion polymerization. In today’s article, we’re looking at the differences between emulsion polymerization and solution polymerization.
Monomers are dispersed in an aqueous phase during emulsion polymerization. This phase generates initiator radicals that migrate into soap micelles full of monomer molecules. As more monomers migrate into the micelle, polymerization continues as a process.
Processes
With only one free radical is present in the micelle prior to termination of the process, you can achieve very high molecular weights of 1 million or more. The viscosity of the medium where the particles are dispersed determines the viscosity of the latex. At the end, the emulsion latex particle is in fact an oil in water emulsion when aqueous.
In solution polymerization, a processor dissolves a monomer in a suitable solvent, along with chain transfer agents and a free radical initiator. The catalyst can be either ionic or a coordination catalyst (either dissolved or suspended. Inert solvents promote viscosity control and proper levels of heat transfer. In many cases, manufacturers use water as the primary solvent.
Applications
Emulsion polymerization is the most widely-used technique for industrial use--processors polymerize monomers such as styrene, butadiene,methyl methacrylate, and vinyl acetate. At Mallard Creek Polymers, we use emulsion polymerization to develop a variety of products for multiple market applications. With emulsion polymerization, we achieve latex particles, a dispersion of polymer in water. With these latex particles as a base material, our customers can add other chemicals to form paints and coatings, adhesives and sealants, nonwovens, paper, print and packaging, construction, and textiles--the possibilities for emulsion polymers are endless. Read the article What’s in a Can? To learn more about formulating coatings based on emulsion polymers
Solution polymerization is a common method for achieving polyacrylic acid (PAA) or polyacrylonitrile (PAN). PAA is a base material for products like disposable diapers, while you’ll find PAN as a raw material for acrylic apparel like socks and sweaters, tents, tennis rackets, and fishing rods. Solution polymers also see a wide range of use in adhesives and coatings.
Advantages and Disadvantages
There are some distinct advantages and disadvantages for each type of polymerization. With emulsion polymerization, you don’t have problems related to chain transfer or heat transfer. The products obtained in latex form are directly usable. With emulsion polymerization, we can achieve a high molecular weight product very quickly--within 1-2 hours. Disadvantages include the fact emulsion polymerization yields a less pure end-product than the slower bulk polymerization. You need a heavy technology investment to recover emulsion polymers in solid form, and the high water use in emulsion polymerization results in a lower yield-per-reactor volume.
There are also advantages and disadvantages to using solution polymerization. With this technique, heat transfer is easy, since solvents are involved. Stirring is also easy, since solution polymerization generates a low viscosity mixture. Mass transfer of the resulting polymer is also easy. The resulting product, while in liquid form, can be used as a solid simply by drying. Manufacturers can’t use solution polymerization to achieve high molecular weights; the presence of a solvent lowers the actual rate of polymerization in the mixture, and complete removal of the solvent is difficult.
Conclusions
There will always be a market for products featuring base monomers polymerized by either emulsion or solution polymerization techniques. We can produce emulsion polymers quickly, and they are the preferred choice of our manufacturing partners who need a high molecular weight raw material for more durable applications like industrial-grade paints and adhesives, as well as construction applications like cement mixtures and asphalt modifiers. Solution polymerization has its place in a wide array of apparel applications as well as other products where molecular weight is less important and lower viscosities are needed for production of coatings and adhesives.
For more information on our lineup of emulsion polymers for multiple market applications, contact Mallard Creek Polymers today.
