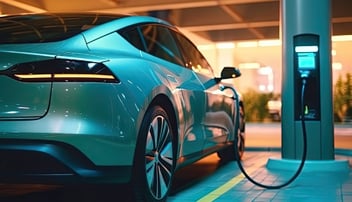
Nitrile elastomers are emulsion polymers produced using rubber polymerization techniques. Also known as nitrile emulsions or nitrile latexes, these are dispersions of acrylonitrile and butadiene — or sometimes styrene — in water. Nitrile elastomers..
Nitrile elastomers are emulsion polymers produced using rubber polymerization techniques. Also known as nitrile emulsions or nitrile latexes, these are dispersions of acrylonitrile and butadiene — or sometimes styrene — in water. Nitrile elastomers are true colloids, defined as a homogenous amorphous substance consisting of large molecules or ultramicroscopic particles of one substance that are distributed through another substance. These spherical particles range in size from 60 to 250 nanometers.
In most emulsion polymerization processes, the solid content (i.e., volume of particle phase to total volume of the dispersion) ranges from 40 to 55 percent, with the remaining part consisting of water and dissolved compounds. Solid content is related to viscosity: in the case of typical industrial products, viscosity remains fairly low for solid volume contents up to 55 percent. Above this limit, the viscosity can increase extremely rapidly as a function of solids content. For nitrile latexes, the solid content ranges from 35 to 53 percent, with the majority under 45 percent, and their viscosity remains low, typically under 50 centipoise (cP), which is the amount of force necessary to move a layer of liquid in relation to another liquid.
Primary Features of Nitrile Latex:
Nitrile elastomers are workhorses in a number of industries because they have desirable properties and because those properties can be manipulated. Nitrile emulsions are known for their superior oil, solvent and caustic resistance, toughness, tear and abrasion resistance, wash durability, elasticity and stretch. The table below summarizes some useful properties and how nitrile elastomers perform:
Nitrile Elastomer Properties | ||||
Property | Excellent | Good | Fair | Poor |
Oil, Gas, and Grease Resistance | • | |||
Non-polar Solvent Resistance | • | |||
Mineral Oil Resistance | • | |||
Wear and Abrasion Resistance | • | |||
Low-temperature Flexibility | • | |||
Compression Set | • | |||
Physical Strength | • | |||
Gas Permeability | • | |||
Water Resistance | • | |||
Chemical Resistance | • | |||
Weather Resistance | • | |||
Ozone Resistance | • | |||
Flame Resistance | • |
The ratio of key monomers (butadiene, acrylonitrile and styrene) influences how these properties are expressed. For example, a higher amount of acrylonitrile provides better oil and solvent resistance but reduces softness and flexibility. In fact, the amount of acrylonitrile used to make nitrile elastomers is so important that the whole family of elastomers is organized into a series of grades based on how much acrylonitrile is present. High acrylonitrile grades contain more than 45 percent acrylonitrile, which produces elastomers with excellent oil/gas/grease resistance but with reduced flexibility and elongation. Medium acrylonitrile grades contain between 30 and 45 percent acrylonitrile, which still have good oil/gas/grease resistance but with added flexibility and softness. And, finally, low acrylonitrile grades contain less than 30 percent acrylonitrile, which have superior flexibility and softness but are far less resistant to hydrocarbons.
Performance Features of Nitrile Latex
Beyond the ratio of acrylonitrile to other monomers, the performance of nitrile elastomers can also be manipulated through other chemical processes and reactions. For example, crosslinking through heat-reactive or carboxylated monomers can enhance toughness, abrasion and chemical resistance. In the former case, crosslinking can be achieved by heating the polymer film to approximately 150°C to 175°C. In the latter case, cross-linking agents, such as melamine formaldehyde, urea formaldehyde, phenolic and epoxy resins, can be introduced. Or, for chemical cross-linking, the process uses zinc oxide or zirconium ammonium carbonate.
Nitrile elastomers can also be vulcanized. Charles Goodyear invented the process of vulcanization in 1839 when he added sulfur and additional ingredients, known as accelerators, to natural rubber at high heat. The result was a rubber with improved durability over a broad temperature range. This same process can be achieved with nitrile elastomers — when they are treated with sulfur, accelerators and heat, they become much more durable.
Chemists can also control nitrile emulsions by manipulating the surfactant system used in their formulation. Latexes made using natural emulsifiers, such as fatty acid and rosin acid-based surfactants, will exhibit superior water resistance and are easily precipitated by cationic salts. This makes these products well suited for gasket manufacturing and specialty papermaking processes. Products made from synthetic surfactants — sulfate and sulfonate — will often exhibit superior mechanical stability, which makes them well-suited for certain paper coatings and other high-shear applications, including asphalt emulsion modification, adhesives, metal coating and textiles.
Applications for Nitrile Latex
Nitrile elastomers are most often used in wet applications like slurry and saturations. They can be used in soft coatings on textiles or paper but are not often used on hard substrates. Other applications include:
- Beater-addition gaskets: slurry binder for pulp-based gasket products
- Abrasion paper: saturant and barrier coating for wet sandpaper market
- Masking tape: automotive-grade masking tape; saturant and barrier
- Coal-tar sealer: additive for coal-tar emulsion; helps with cure and flex as well as a thickener
- Friction paper: paper used to laminate onto clutch rings in transmissions
- Paper: printer blanket backing, wing-walk paper
- Abrasion textiles: saturation of cloth or non-woven for sanding products
- Textile coatings: firehose, saturation, polishing, and buffing cloth
- Nonwoven textile: various dipping or spray bonding non-woven fabric
- Resorcinol Formaldehyde Latex (RFL) dip: dipping fabric or yarn for conveyor belt or fluid hose
- Wet lamination adhesive: brakes, tape, lamination, rubber to metal
- Aviation maskant: temporary peelable coating for airplane parts
Some nitrile elastomers have compliance with either or both of the FDA 175.105 and 177.2600 paragraphs. The former deals with materials suitable for indirect food contact for adhesive applications when separated by a functional barrier; the latter concerns rubber articles with repeated use, such as hoses, conveyor belts, pressure cooker seals, and others.
Learn More
Mallard Creek Polymers can work with you to find a nitrile elastomer that fits your application requirements. Contact us today to discuss how we can help.
