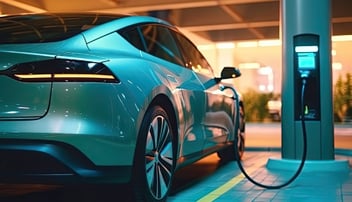
Glass certainly seems like a solid substance — it’s hard and brittle at room temperature — but glass exhibits other properties that make it unique, which is why chemists classify it as an amorphous solid. Amorphous solids are those that have..
Glass certainly seems like a solid substance — it’s hard and brittle at room temperature — but glass exhibits other properties that make it unique, which is why chemists classify it as an amorphous solid. Amorphous solids are those that have short-range order but no long-range order. In this case, order refers to how the atoms in the material are arranged, and in glass, the atoms are not arranged in a definite lattice pattern. Instead, they are loosely networked together so that the distances between atoms can vary substantially, unlike in crystalline materials, where atomic distances are much more consistent.
Of course, glass is not a polymer, though its behavior can be useful in understanding how polymers work (we even use terms like “glass transition” and “glassy state” when discussing polymers, as we’ll see in the next section). Just as traditional, non-polymeric solids can be classified as crystalline and amorphous, so too can polymers. Amorphous polymers, as you might expect, also have no short-range order, but instead of thinking about individual atoms, we need to think about long chains of atoms, which is a defining characteristic of polymers. Given that distinction, we would say the chains in amorphous polymers are randomly tangled, like a plate full of cooked spaghetti noodles. Chains in crystalline polymers align in orderly folded stacks, known as lamellae. Lamellae bring long-range order to polymers, which is more like the orderly arrangement of atoms in typical crystals.
In this article, we will explore the characteristics of amorphous polymers, which are an important class of materials that are used in a number of commercial products, including latex binders and adhesives— the focus of Mallard Creek Polymers.
Glass Transition Temperature
One of the most important characteristics of amorphous polymers is glass transition temperature (Tg). Glass transition temperature is similar to melting point, but it’s not exactly the same. A melting point is generally a discrete temperature, indicating when a material transitions from the solid phase to the liquid phase. For example, the melting point of polypropylene, a crystalline polymer, is 175°C (347°F).
Glass transition temperature refers to the temperature at which a polymer changes from a glassy state to a rubbery state. The glass transition temperature of a specific polymer may be listed as a single temperature, but this value represents a range, with beginning and end temperatures that can extend more than 10 degrees in between. The glass transition temperature affects how a finished polymer will behave, so it’s extremely important. Let’s look at a couple of examples:
- First, let’s consider a polystyrene polymer that has a high Tg around +105°C (220°F). A polystyrene polymer would be in a glassy state until about 100° At room temperature, which is approximately 25°C (77°F), the polymer would be hard, brittle and strong. At the atomic level, we would see very little motion around the bonds holding the atoms together. As the temperature approaches 100°C, the motion around the bonds would increase, and the material would start to become less glass-like and more rubber-like.
- Next, let’s consider a polybutadiene polymer with a low Tg, say -85°C (-121°F). Now we would see something a little different. Room temperature would be far higher than its glass transition temperature, so at 25°C, the polymer would be softer, rubbery and elastic. And there would be significantly more motion around the atomic bonds. To get to this polymer’s glassy state, we would need to reduce the temperature below -85°C, which is quite cold.
It should also be noted that some polymers aren’t completely amorphous — they are part crystalline and part amorphous. We’ll cover this in the next section.
Amorphous vs. Crystalline
Most amorphous polymers are not completely amorphous. At the same time, most crystalline polymers aren’t completely crystalline. Chemists often refer to a polymer’s degree of crystallinity to describe where it sits along this spectrum. Crystallinity can range from 0 percent (entirely amorphous) to 100 percent (entirely crystalline), but most polymers fall somewhere between those extremes. It’s important to know this because the physical properties of a polymer, such as density, ductility, and yield strength, are all highly dependent on how amorphous or crystalline it is.
Chemists use a variety of techniques to measure the degree of crystallinity in polymers. These include taking density measurements, conducting thermal analysis and studying X-ray diffraction patterns. Each of these methods relies on different principles, which means the measurements can be slightly different. As a result, researchers often collect data using more than one technique to confirm the appropriate range of crystallinity and to account for discrepancies.
Characteristics of Amorphous Polymers
The molecular structure of a polymer — and the degree of crystallinity — has a tremendous impact on its properties. For example, crystalline polymers are generally opaque because the folded chains packed in the lamellae act to reflect light. Amorphous polymers, with their random entanglement of chains, tend to let light pass through them. As the percentage crystallinity increases, the polymer becomes progressively less transparent.
There are other important characteristics of amorphous polymers, and chemists use a variety of techniques to determine them. Let’s review three of the most common methods:
Glass Transition Temperature using thermal analysis via differential scanning calorimetry, or DSC: A differential scanning calorimeter measures the flow of heat into or out of a material with respect to time or temperature. In DSC, the polymer sample is placed in the device and cooled well below its expected glass transition temperature and heated to a high temperature. A computer attached to the system measures the thermal response of the polymer, producing a plot of heat flow versus temperature. As the temperature goes across the glass transition, the heat flow into the sample increases. The midpoint temperature of this heat flow change is considered the glass transition temperature.
Dynamic Mechanical Analysis, or DMA: A dynamic mechanical analyzer applies a force to a polymer sample over a small oscillatory displacement and measures the response across a temperature range. DMA provides valuable information on the stiffness and deformability of a polymer. In its glassy state, a polymer requires much higher force to make the same oscillatory movement compared to its rubbery state. This resistance to applied force is called elastic modulus. The change in modulus over temperature from high glassy to low rubbery is another measurement for glass transition temperature. DMA also provides information about the viscous and elastic behavior of a polymer. The difference between the applied force and measured response relates to the malleability. The lower the measured response compared to the applied force, the more liquid-like (viscous) and less solid-like (elastic) the polymer is.
Tensile Strength and Elongation: A tensile testing machine pulls a strip of polymer film and measures the force required. As the film is extended, the force required to pull typically increases until it reaches a maximum that is referred to as the tensile strength. The film is extended all the way until breaks, and that break distance is used to calculate the percent elongation at break.
By studying amorphous polymers using these and similar techniques, chemists can build a profile of the category. Here are some of the common properties of amorphous polymers:
- They exhibit relatively low resistance to heat.
- Because they have a randomly ordered molecular structure that lacks a sharp melting point, they soften gradually as the temperature rises.
- They are not prone to shrinkage as they cool.
- Their end-use behavior is very dependent on the application’s temperature being above or below the glass transition temperature.
- They are tough and brittle at low temperatures, but they lose their toughness quickly above their glass transition temperature and become malleable and prone to elongation.
- Due to their deformability, they can bond well to substrates.
- They often need to be applied and dried above their glass transition temperature, or minimum film formation temperature (MFFT) to avoid defects in the final material. For example, if the drying temperature is below the MFFT, then a discontinuous film or powder compact may form. See our article on film formation to learn more.
This is not an exhaustive list, but it demonstrates how useful and versatile amorphous polymers can be when their properties are carefully considered and controlled. Depending on their precise design, amorphous polymers can be customized for a wide range of applications in the nonwovens, adhesives, textiles, printing and packaging, paints and coatings, construction and paper industries.
Amorphous Polymer Specialists
Mallard Creek Polymers specializes in the design and manufacturing of amorphous polymers. We work with customers to understand their design and engineering challenges and to develop emulsion polymers that address those needs, tweaking properties based on the intended application. Contact us for more information.
