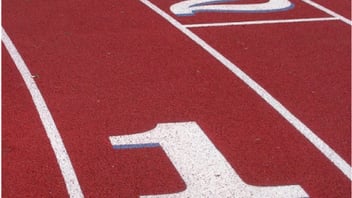
As explained in the “Introduction to Polymer-Modified Concrete,” when polymers are added to concrete, the resulting material is known as polymer-modified concrete (PMC), polymer cement concrete (PCC) or, when it’s used specifically on bridge..
As explained in the “Introduction to Polymer-Modified Concrete,” when polymers are added to concrete, the resulting material is known as polymer-modified concrete (PMC), polymer cement concrete (PCC) or, when it’s used specifically on bridge decking, as latex-modified concrete (LMC). The many advantages of using PMC, PCC and LMC have been proven across a broad range of applications and industries.
Polymers can greatly enhance the performance of concretes, making it stronger and more durable while making it easier to work with during construction; increasing its resistance to water permeability; increasing its stability in extreme weather; and improving its resistance to chemicals.
When you think about construction that could benefit from polymer-modified concrete, you often imagine building big — tunnels, precast bridges, skyscrapers, culverts, slabs and stormwater runoff retention chambers. PMC is ideal for these applications because it can be formed into many shapes and because it offers superior strength, especially when reinforced with steel rebar. But PMC is a flexible material that has many uses other than forming large structural elements. Some of these applications include:
- Bridge Decking — Because of its many benefits, latex-modified concrete (or LMC) is becoming a popular choice for bridge decking applications.
- Surface Overlays — The attractive advantages of using PMC as an overlay material for airport surfaces, bike and bus lanes and other large-scale applications justify its sometimes-higher cost.
- Road Surfacing — Polymer-modified road surfaces provide significant advantages over other methods of road construction, when the environmental impact, cost reduction, cure time and the benefits of use of native soils and aggregates to provide a natural appearance are all taken into consideration.
- Floor Toppings — When used in both industrial and decorative concrete floor toppings and overlays, polymers help thin cementitious toppings hold together, adding strength and/or flexibility to the application.
- Concrete Repairs and Patching — PMC works well to repair stone and concrete architectural elements and to provide a fast-curing, high-strength patching material suitable for use in the repair of hydraulic cement concrete structures.
Cutting-edge Applications of PMC
Over the past 15 to 35 years, scientists and engineers have developed some exciting new high-performance applications for PMC, taking the technology to the next level and creating solutions to some of the biggest challenges in the construction industry. Here are four of the most notable innovations:
- Self-consolidating concrete (SCC), also known as self-compacting concrete, was developed in Japan in the 1980s for the construction of high-rise buildings, bridges and tunnels. A high-performance material that is stronger and more durable, it delivers more reliable quality and a more uniform surface texture and enables faster construction.
Ordinary concrete is a dense, viscous material that requires the use of vibration or other mechanical consolidation techniques to remove air bubbles that have been trapped during pouring, which will weaken the concrete if left in place. However, using vibration is time- and labor-intensive, and if not performed correctly, can lead to critical construction defects. SCC is designed to avoid this problem. It is made by combining a high proportion of fine aggregate, polycarboxylate polymers and viscosity-modifiers. Recently, some engineers have experimented with the addition of latex to various types of superplasticizers to make an updated version of SCC. Either way, the result is a stable, highly flowable, self-consolidating concrete, which means it spreads into concrete formwork by its own weight, without the need for vibration equipment. Using SCC reduces labor and time and eliminates a possible source of technical and quality control issues. - Pervious concrete, also known as no-fines or no-sand concrete, is another cutting-edge application of polymer-modified concrete. Because the formulation for pervious concrete does not use sand, it has a porous, open-cell structure that readily lets water pass through, making it an optimal material for managing stormwater runoff in built environments in accordance with U.S. Environmental Protection Agency (EPA) regulations. With pervious concrete, latex functions as an enhancer, helping to bind the aggregates together. The use of styrene-butadiene polymers in pervious concrete can improve its mechanical performance, particularly flexural strength, without reducing void content and drainability.
The one drawback to pervious concrete is the industry’s general lack of experience with the material. In pervious concrete, the amounts of water, cementitious materials and other ingredients must be carefully controlled to achieve the desired results. - Cementless concrete is an emerging technology that is attracting attention for its potential as a sustainable building material. The production of Portland cement requires significant amounts of energy to produce. At the same time, the cement in finished structures generate its own carbon dioxide. Production of one ton of cement produces about one ton of CO2, which represents approximately 5–7% of the global greenhouse gas produced annually. Reducing the amount of cement used in concrete presents a viable opportunity to decrease the carbon footprint of built environments.
Engineers have experimented with silica fume, fly ash and slag as supplementary cementing materials in daily concrete production and have been able to reduce CO2 emission. Research is still ongoing, but latex admixtures hold promise as materials to replace cement, as well.
- Bendable concrete, or Engineered Cementitious Composite (ECC), is another relatively new application of PMC. Traditional concrete has good load-bearing capacity, but it cannot withstand tensile stresses effectively. By replacing the coarse aggregate in concrete with fibers, concrete can be made more flexible, even bendable. The fibers can take many forms — silica fibers, glass fibers, steel fibers, asbestos fibers or polyvinyl alcohol fibers — but it’s the elasticity of the microfibers that imparts flexibility to the concrete. Another important element in bendable concrete is microsilica sand, though fine river sand can also be used. Superplasticizers supplemented with latex are also used to improve the flexibility of the concrete even more.
Currently, bendable concrete is expensive — about four times the cost of regular concrete. But as researchers experiment with different formulations, the costs are coming down. A team at Louisiana State University recently introduced their version of bendable content that reduced the ECC cost by half.
Let’s Collaborate on Concrete Applications
At Mallard Creek Polymers, our technical experts specialize in the design and manufacturing of emulsion polymers for a wide range of applications, including polymer-modified concrete for the construction market. Even if you have a specialty need or a cutting-edge application such as cementless concrete, we will work with you to understand your design and engineering challenges and to formulate polymers that address those needs. Contact us for more information.
